How Does A Tandem Gear Pump Work
In the world of hydraulic systems, the tandem gear pump plays a pivotal role in powering various machinery and equipment. This reliable and efficient component has been a cornerstone of hydraulic technology for decades, and understanding how it works is essential for those in the industry. In this comprehensive article, we will delve into the intricacies of tandem gear pumps, shedding light on their operation, applications, and importance in the hydraulic industry.
Introduction to Tandem Gear Pumps
Tandem gear pumps are a type of positive displacement pump used extensively in hydraulic systems. They are designed to generate fluid flow by trapping and displacing a fixed amount of fluid with each revolution of the gears. These pumps are particularly favored for their simplicity, reliability, and versatility, making them indispensable in numerous industrial applications.
The purpose of hydraulic series pumps is to obtain different flow rates. Two pumps of different specifications are connected in series, so that three hydraulic oil flow rates can be obtained. In this way, the speed of the hydraulic actuator can be easily adjusted. In the hydraulic industry, connecting hydraulic pumps in series, in addition to obtaining different flow rates for speed regulation, can also be used for different specifications of pumps, different pressures can be applied to achieve such a purpose as high pressure and small flow pressurization, low pressure and high flow fast feeding. From this structural point of view, it can not only change and simplify the design of the hydraulic system, but also achieve the purpose of energy saving.
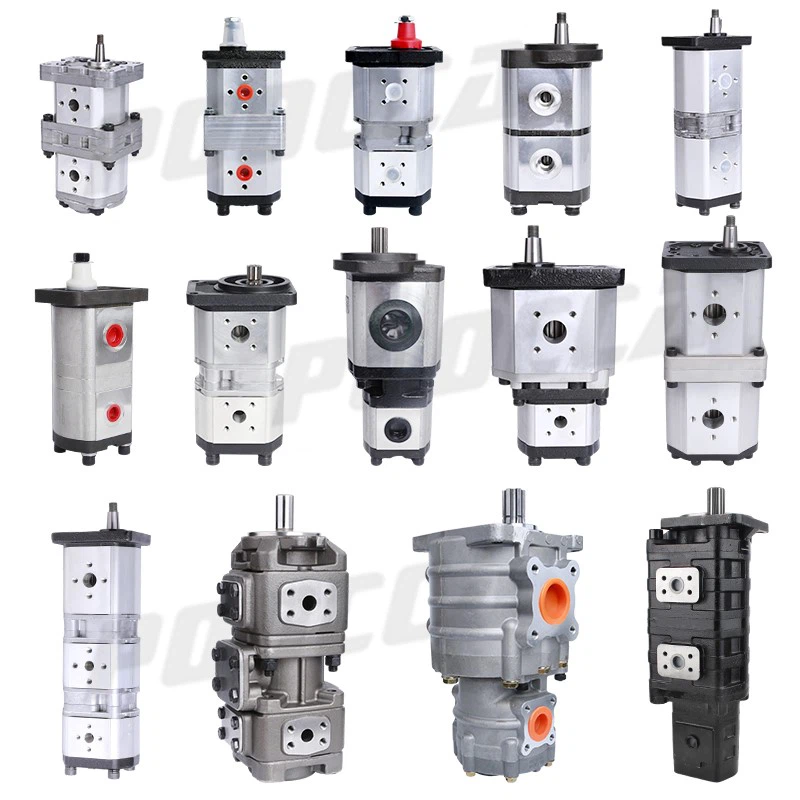
Working Principle of Tandem Gear Pump
Tandem gear pump operate on the principle of positive displacement, which means they displace a fixed volume of fluid per revolution. The main components of a tandem gear pump include two meshing gears, an inlet port, an outlet port, and a casing.
Gear Assembly: Tandem gear pumps consist of two gears – a driving gear (connected to the input shaft) and a driven gear. These gears are closely meshed, with a small gap between their teeth.
Inlet and Outlet Ports: The pump has an inlet port and an outlet port, which allow the entry and exit of hydraulic fluid, respectively.
Casing: The gears are housed within a casing that contains the hydraulic fluid. The casing provides support and maintains the necessary clearances between the gears and the casing walls.
Step-by-Step Operation
Fluid Intake: When the pump is in operation, hydraulic fluid enters through the inlet port. The gears rotate in opposite directions, causing the fluid to be trapped in the spaces between the gear teeth and the casing walls.
Fluid Displacement: As the gears continue to rotate, the trapped fluid is carried along with the rotating gears. The fluid is displaced from the inlet side to the outlet side of the pump.
Fluid Exit: When the fluid reaches the outlet port, it is forced out of the pump and into the hydraulic system, where it can be used to perform work.
Sealing: Proper sealing is essential to prevent leakage between the high-pressure outlet side and the low-pressure inlet side of the pump. Sealing is achieved through the close tolerance between the gears, as well as the use of gaskets and seals within the pump.
Tandem gear pumps offer several advantages that make them a popular choice in hydraulic systems:
Advantages of Tandem Gear Pump
Reliability: Tandem gear pumps are known for their durability and longevity. They can handle a wide range of operating conditions and are less susceptible to damage from contamination in the hydraulic fluid.
Efficiency: These pumps have a relatively high volumetric efficiency, meaning they can deliver a consistent flow of hydraulic fluid even at varying pressures.
Compact Design: Tandem gear pumps are compact and can deliver significant hydraulic power in a relatively small package, making them suitable for various applications where space is limited.
Cost-Effective: They are cost-effective compared to some other types of hydraulic pumps, making them a practical choice for many industries.
Applications of Tandem Gear Pumps
Tandem gear pumps find application in a wide range of industries and machinery, including but not limited to:
Construction Machinery: Tandem gear pumps are used in excavators, bulldozers, and other heavy equipment to power hydraulic systems for digging, lifting, and moving materials.
Agricultural Machinery: Tractors, combines, and other farm equipment often rely on tandem gear pumps to operate hydraulic systems for functions such as steering and lifting.
Material Handling: Conveyor systems, forklifts, and pallet jacks utilize tandem gear pumps to control lifting and movement functions.
Automotive Industry: Tandem gear pumps are employed in power steering systems to assist drivers in turning the steering wheel with ease.
Industrial Machinery: Various manufacturing and industrial machines use tandem gear pumps for tasks such as clamping, pressing, and shaping materials.
In the ever-evolving world of hydraulic systems, tandem gear pumps continue to be a cornerstone of reliable and efficient fluid power. Their straightforward design and positive displacement principle make them invaluable in a wide range of applications, from heavy construction equipment to precision industrial machinery. As industries continue to advance, tandem gear pumps remain a vital component, ensuring the smooth operation of hydraulic systems worldwide. Understanding their working principle and advantages is crucial for anyone involved in the hydraulic industry, where efficiency and reliability are paramount.
azpff,azpgf,alp+alpp,ghp+ghpp,nsh+nsh, etc
For more double hydraulic gear pump products, please contact poocca. We will reply to you as soon as possible and send you relevant product preferential quotations, parameter information, pictures and other content. We look forward to cooperating with you.